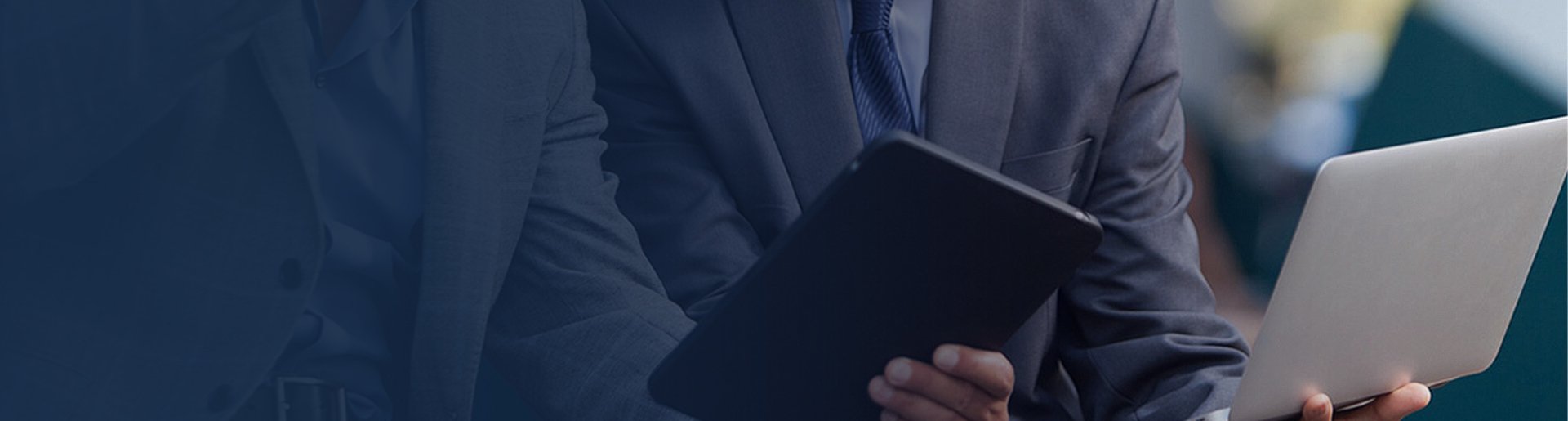
Continuous die vs. single-process die: How to choose the best stamping solution?
With 28 years of experience in metal manufacturing, Kailai Machinery analyzes the stamping process for you
As a professional custom metal parts manufacturer established in 1996, Kailai Machinery has accumulated rich experience in the field of metal manufacturing, focusing on precision stamping, stretching, welding and surface treatment. In the stamping process, the choice of mold directly affects production efficiency and cost. This article will deeply analyze the advantages and disadvantages of continuous molds and single-process molds to help customers optimize production decisions.
Continuous mold: the first choice for efficient mass production
Core advantages
1. High efficiency: The continuous mold can complete multiple processes such as punching, bending, and forming at one time through multi-station synchronous operation, greatly improving production capacity, especially suitable for large-volume orders.
2. High precision: Since the material is continuously fed into the mold, the positioning error is small, and the product consistency is better than the single-process mold.
3. Low cost: Although the initial investment in the mold is high, the unit cost is significantly reduced when it is amortized to mass production.
Applicable scenarios
- Electronic appliances: such as heat sinks, connector terminals and other precision small parts.
- Automotive parts: Standardized parts such as seat belt buckles and brackets
- Daily hardware: such as buttons, metal fasteners, etc.
Single process mold: Flexible response to small batch customization
Core advantages
1. Low initial cost: The mold structure is simple and the development cycle is short, which is suitable for small batch trial production or customized needs.
2. High flexibility: A certain process (such as punching or bending) can be adjusted separately, which is convenient for process optimization.
3. Adapt to complex materials: More friendly to stamping of high hardness or special alloys (such as stainless steel), reducing mold wear.
Applicable scenarios
- Sample development: Avoid high mold investment in the new product verification stage.
- Large size parts: such as chassis shells, large sheet metal parts, continuous molds may be limited by machine tool size.
- Non-standard customization: such as artistic decorative parts and special-shaped structural parts.
Kailai Machinery's solution: matching needs and optimizing production
With 28 years of experience in metal manufacturing, we provide customers with one-stop services from mold design to mass production delivery:
- Continuous die stamping: using high-precision CNC machine tools to ensure the stability of large-volume orders.
- Single-process mold customization: quickly respond to small-batch needs and support material diversification (stainless steel, aluminum alloy, etc.).
- Surface treatment matching: provide electroplating, spraying, anodizing and other processes to improve product durability.
Choose Kailai Machinery and let professional stamping technology empower your products!