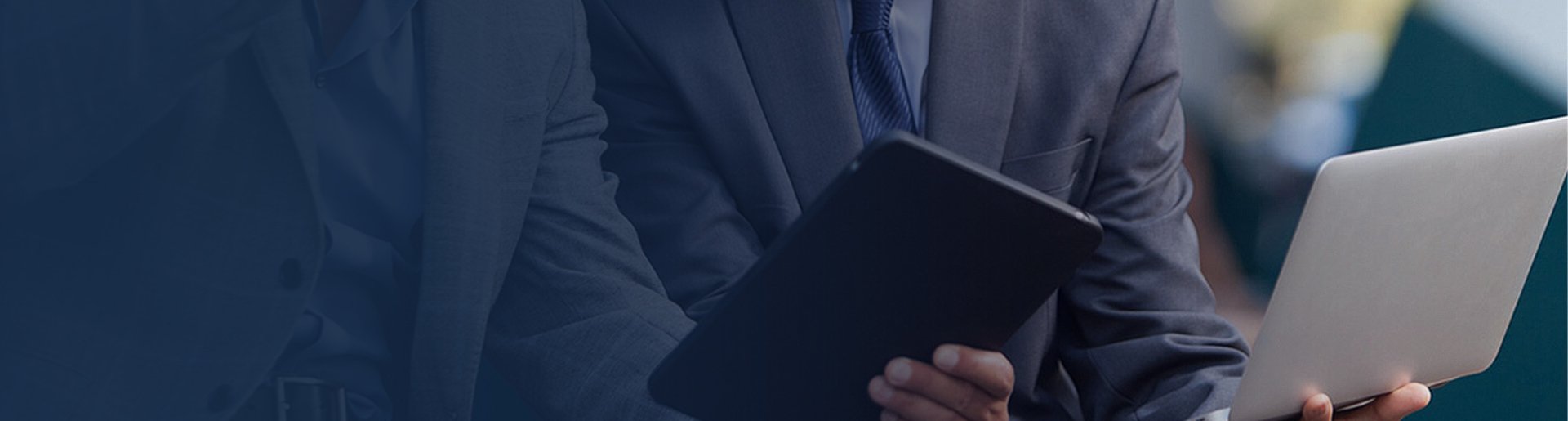
Kailai Machinery helps you solve - in-depth analysis and solution strategies for the springback problem in metal stamping
In the field of metal manufacturing, metal stamping is a key processing technology widely used in various industries. Since its establishment in 1996, Kailai Machinery, as a dedicated Chinese custom metal parts manufacturer, has always been committed to providing customers with high-quality metal stamping, stretching, welding and common surface treatment services, among which metal stamping is our core business. In long-term production practice, we have a deep understanding of the complexity and importance of the springback problem in the metal stamping process.
Springback phenomenon and its impact
Springback is an issue that cannot be ignored in the metal stamping process. Simply put, when the metal sheet undergoes plastic deformation under the action of the stamping die, once the external force is removed, the material will produce a certain degree of elastic recovery due to its own elastic properties, resulting in a deviation between the final shape of the stamped part and the designed shape. This deviation may seem small, but it may have a significant impact on product quality. In some fields with extremely high precision requirements, such as aerospace, automobile manufacturing, etc., springback may cause parts to fail to meet assembly requirements, increase scrap rate, and thus increase production costs and delay production cycles.
Reasons for springback
1. Influence of material properties
Different metal materials have different elastic limits and yield points. Taking steel and aluminum alloy as examples, the elastic modulus of steel is relatively high and the yield strength is also large, which makes the springback of steel relatively small during stamping; while the elastic modulus of aluminum alloy is low and the yield strength is also weak, and its springback phenomenon is often more obvious. Factors such as the chemical composition and organizational structure of the material will also affect the springback. Steel with a high carbon content has relatively high hardness and strength, and the springback will also be different.
2. The role of stamping parameters
Parameters such as pressure, speed and temperature in the stamping process have a direct impact on the springback. When the stamping pressure is insufficient, the metal sheet cannot be fully deformed, and a large springback will occur after unloading; while excessive stamping pressure may cause excessive deformation of the material or even rupture. If the stamping speed is too fast, the material will be subjected to a large impact force in a short period of time, resulting in uneven deformation, thereby increasing the possibility of springback. The influence of temperature on springback cannot be ignored. When stamping in a high temperature environment, the yield strength of the material decreases and the plasticity increases, but it may also cause increased springback.
3. The key role of mold design
The shape, processing accuracy and finishing of the mold are important factors causing springback. If the parameters such as the fillet radius and gap size of the mold are not designed properly, the metal sheet will be unevenly stressed during the stamping process, resulting in springback. Insufficient mold processing accuracy, large surface roughness, dimensional deviation and other problems will also affect the quality of stamped parts and increase the risk of springback.
Kailai Machinery's solution strategy
1. Optimize mold design
Kailai Machinery has a professional technical team and rich experience in metal stamping. It will carefully design molds according to different stamping parts shapes and material properties. By reasonably adjusting the mold's fillet radius, gap size and other parameters, the metal sheet can be more evenly stressed during the stamping process, effectively reducing springback. We will also use advanced mold manufacturing technology to improve the mold's processing accuracy, ensure that the mold surface is smooth and the size is accurate, thereby reducing the possibility of springback.
2. Adjust stamping parameters
In actual production, we will accurately adjust parameters such as stamping pressure, speed and temperature according to the characteristics of the material and the requirements of the stamping parts. Through multiple tests and optimizations, we find the best combination of stamping parameters so that the metal sheet can be fully deformed while minimizing springback as much as possible. For some materials that are prone to springback, we will appropriately increase the stamping pressure and reduce the stamping speed to improve the precision of the stamping parts.
3. Choose the right material
On the premise of meeting the product performance requirements, we will give priority to metal materials with smaller springback. For some stamping parts with extremely high precision requirements, we will use high-quality high-strength steel. Although the cost is relatively high, it can effectively reduce springback and improve product quality. We will also provide reasonable material selection suggestions based on customer needs and budgets.
4. Use compensation method
According to the springback amount obtained by pre-calculation or actual measurement, the relevant dimensions are reversely corrected during mold design so that the stamping parts can reach the shape and size required by the design after springback. This method requires accurate prediction and control of the springback amount. We will use advanced simulation software and actual production experience to continuously optimize the compensation plan.
Since its establishment in 1996, Kailai Machinery has been deeply involved in the field of metal stamping. With rich experience and professional technology, it has successfully solved the springback problems encountered by many customers in the metal stamping process. Whether it is a complex shape or high-precision requirements, we can provide customized solutions to meet customer needs. We have advanced production equipment and a strict quality inspection system. From raw material procurement to product delivery, every link is strictly controlled to ensure stable and reliable product quality.
In the future development, Kailai Machinery will continue to uphold the concept of professionalism, innovation and efficiency, and continuously improve its technical level and service quality. We will increase investment in the research and development of metal stamping technology, explore more new methods and technologies to solve the springback problem, and provide customers with better metal parts manufacturing services. If you have any needs in the field of metal manufacturing, please feel free to contact us. We look forward to working with you to create a better future.