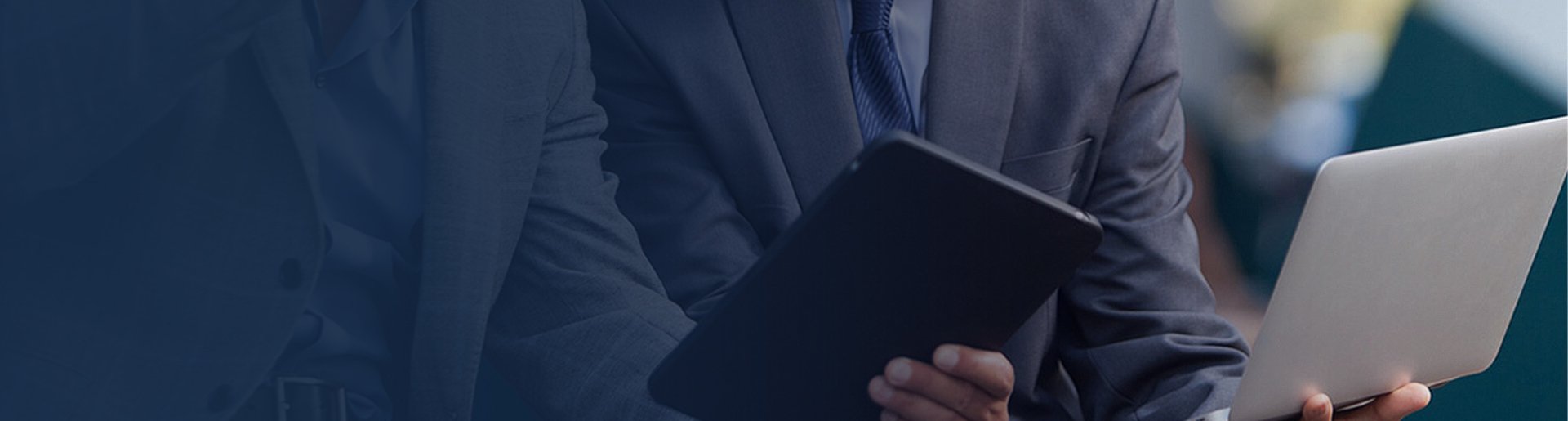
Metal stamping tear prevention guide: 28 years of experience sharing
In the field of metal manufacturing, metal stamping is a widely used and critical process. As a Chinese custom metal parts manufacturer with 28 years of rich experience, Kailai Machinery knows that in the metal stamping process, avoiding material tearing is the key to ensuring product quality and production efficiency. This article will explore in depth how to effectively avoid material tearing during forming in metal stamping, and provide practical suggestions and methods for industry practitioners.
1. Understanding material properties is the basis
Different metal materials have different properties, such as hardness, ductility, yield strength, etc. Before metal stamping, it is important to fully understand the properties of the materials used. For example, some aluminum alloy materials have good ductility but relatively low hardness; while stainless steel materials have high hardness, but may require greater stamping force during stamping. After understanding the material properties, we can adjust the stamping process parameters according to its characteristics to reduce the risk of material tearing.
Taking our actual production experience as an example, when processing an aluminum alloy plate, through the analysis of its material properties, we appropriately reduced the stamping speed and increased the number of stampings, so that the material can be deformed evenly during the forming process, effectively avoiding the occurrence of tearing.
2. Reasonable design of stamping die
The design of the stamping die has a direct impact on the tearing of the material. Factors such as the gap, edge shape and fillet radius of the die need to be precisely controlled.
1. Optimize the die gap: If the die gap is too large, the material will be subjected to greater tensile stress during the stamping process, which is easy to cause tearing; if the gap is too small, it may increase the wear of the die and even damage the die. Generally speaking, the double-sided stamping gap of fine blanking is about 1%-1.5% of the material thickness, so that the material can always remain perpendicular to the stamping direction, reduce the bending deformation of the deformation zone, and do not generate tensile stress, which constitutes the conditions for compressive stress plastic deformation. In actual production, we will accurately calculate and adjust the die gap according to different materials and stamping requirements to ensure the smooth progress of the stamping process.
2. Design reasonable edge shape and fillet radius: Make the die or punch edge into a very small fillet, generally with a fillet radius of 0.05mm - 0.1mm, to reduce stress concentration at the edge and avoid or delay the generation of cracks. At the same time, a reasonable edge shape can make the material evenly stressed during the stamping process and reduce the possibility of tearing.
3. Control stamping process parameters
1. Adjust the stamping speed: Too fast a stamping speed may cause excessive local stress on the material, thereby causing tearing. In actual operation, the stamping speed should be appropriately adjusted according to the characteristics of the material and the design of the mold so that the material can deform smoothly during the stamping process. For some materials with poor ductility, we usually reduce the stamping speed to allow the material enough time to adapt to deformation.
2. Reasonably apply the blanking force and the counter pressure of the ejector: Use the blanking force and the counter pressure of the ejector to tightly press the deformation area of the material so that it is in a two-way pressure state, and increase the hydrostatic pressure of the material in the deformation area to improve the plasticity of the material and inhibit the generation of cracks and tearing. However, the greater the blanking force and counter pressure, the better. Excessive pressure may increase the load on the mold and shorten the service life of the mold. Therefore, it is necessary to debug according to the specific situation in actual production to find the best pressure value.
4. Use advanced stamping technology
With the continuous development of science and technology, some advanced stamping technologies have emerged, such as fine blanking technology. Fine blanking is a non-cutting processing technology, which is a precision blanking method developed on the basis of ordinary stamping technology. This processing method can make the punching surface of the punching part free of cracks and tears throughout its entire material thickness, and can achieve the most stringent dimensional accuracy and straightness tolerance. During fine blanking, the gear ring pressure plate presses the material against the die through force, thereby generating lateral side pressure on the inner surface of the V-shaped tooth to prevent the material from tearing in the shearing zone and the lateral flow of the metal; while the punch presses the material, the material is pressed by the counter pressure of the ejector, and the stress concentration is eliminated by using the extremely small gap and the rounded die edge, so that the metal in the shearing zone is in a three-dimensional compressive stress state, eliminating the tensile stress in the zone, improving the plasticity of the material, and fundamentally preventing the bending, stretching, and tearing phenomena that occur in ordinary blanking. Our company actively adopts fine blanking technology in the production of some products with high precision and quality requirements, and has achieved good results.
In the process of metal stamping, avoiding material tearing requires understanding material properties, rationally designing molds, controlling process parameters, and adopting advanced technologies. As a custom metal parts manufacturer with 28 years of experience, Kailai Machinery has always been committed to continuously optimizing metal stamping processes and providing customers with high-quality metal parts products. I hope that the content shared in this article can be helpful to my peers and jointly promote the development of the metal manufacturing industry.