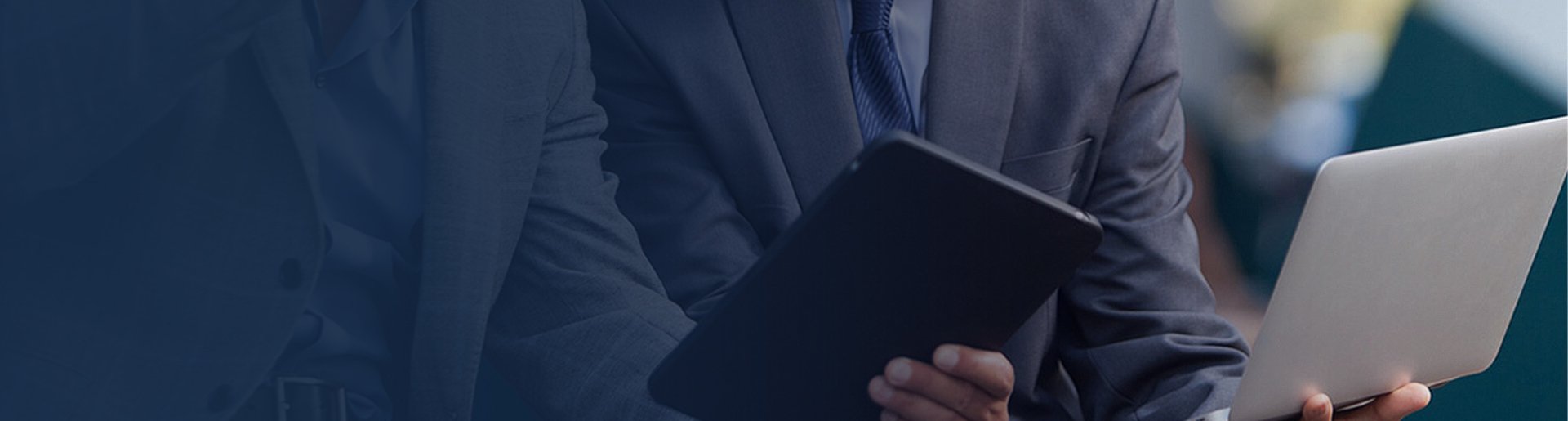
With 28 years of experience in metal manufacturing, Kailai Machinery will analyze the core application of welding fixtures in welding for you
In the field of metal manufacturing, welding is the core process of connecting metal components, and its quality and efficiency directly determine the performance and market competitiveness of the product. As an indispensable auxiliary device in the welding process, welding fixtures have always been the key link to ensure process stability in our 28 years of experience in metal manufacturing.
Welding fixtures: the core support of welding process
The essence of welding fixtures is to provide rigid constraints for the welding process through precise positioning and stable clamping. In metal manufacturing, the heat input during welding will cause the material to expand and contract. If there is a lack of effective constraints, it is very easy to cause component displacement and deformation, which will lead to problems such as weld deviation and insufficient strength. The existence of welding fixtures is to fix the components to be welded in the preset position through the pre-set positioning reference and clamping force, ensure that the weld trajectory meets the design requirements, and lay the foundation for high-quality welding.
Three core values of welding fixtures to welding process
1. Ensure welding accuracy and improve product consistency
In precision metal manufacturing, accuracy is the lifeline of product quality. The welding fixture controls the relative position error of the components to the micron level through mechanical positioning structures (such as positioning pins, V-blocks, blocks, etc.), ensuring that key indicators such as the position and symmetry of the weld meet the design standards. Especially in multi-batch customized production, unified welding fixtures can effectively reduce the accuracy fluctuations caused by differences in manual operations and ensure the consistency of each product. This is also one of our core competitiveness in providing supporting parts for the high-end equipment manufacturing field for a long time.
2. Optimize welding process and improve production efficiency
In traditional welding, the positioning, adjustment, and clamping of components often consume a lot of manual time, accounting for more than 40% of the entire welding cycle. The welding fixture realizes "one clamping, multiple welding" through integrated design, which greatly shortens the auxiliary time. At the same time, the stable clamping state allows welders to focus on weld formation control without frequently adjusting the component position, which indirectly increases the welding speed. In our production practice, the reasonable application of welding fixtures can increase welding efficiency by more than 30% and quickly respond to customer delivery requirements.
3. Control welding stress and reduce deformation defects
During the welding process, local high temperature will produce uneven thermal stress, which is the main cause of component deformation. The welding fixture offsets part of the thermal stress by applying reverse preload to the component; at the same time, the rigid constraint limits the free contraction of the component, guides the deformation to the preset direction, and facilitates subsequent correction. For scenes prone to high stress such as thick plate welding and welding of dissimilar materials, special welding fixtures are indispensable - it can avoid the scrapping of parts due to deformation and reduce production costs.
Our welding fixture technology practice
With 28 years of metal manufacturing experience, Kailai Machinery has formed a unique advantage in the design and application of welding fixtures. We always adhere to the concept of "fixture adaptation process" rather than simply applying standard parts:
For high-strength steel welding, we will calculate the clamping force according to the yield strength of the material to avoid excessive pressure causing plastic deformation of the component; for thin-walled parts welding, a flexible clamping structure is used to disperse stress through buffer materials to prevent parts from crushing. At the same time, we integrate digital design into fixture development, use 3D modeling software to simulate the assembly relationship between fixtures and components, predict interference risks in advance, and ensure the coordination of fixtures with welding robots, positioners and other equipment.
In customized projects, we often use modular welding fixtures - through standardized basic modules (such as guide rails and brackets) with replaceable positioning components, we can quickly combine fixture solutions that are suitable for different parts, which not only reduces customization costs but also shortens the fixture development cycle. This flexible solution allows us to efficiently undertake small batches and multiple varieties of customized orders and maintain flexible response capabilities in the fierce metal manufacturing market.
In the future, as metal manufacturing is upgraded to intelligence and precision, the requirements for fixtures in welding processes will be more stringent. Kailai Machinery will continue to integrate years of practical experience and new technologies to develop new fixtures suitable for automated welding and laser welding, create higher value for customers with more accurate and efficient welding solutions, and consolidate its leading position in the field of customized metal parts.