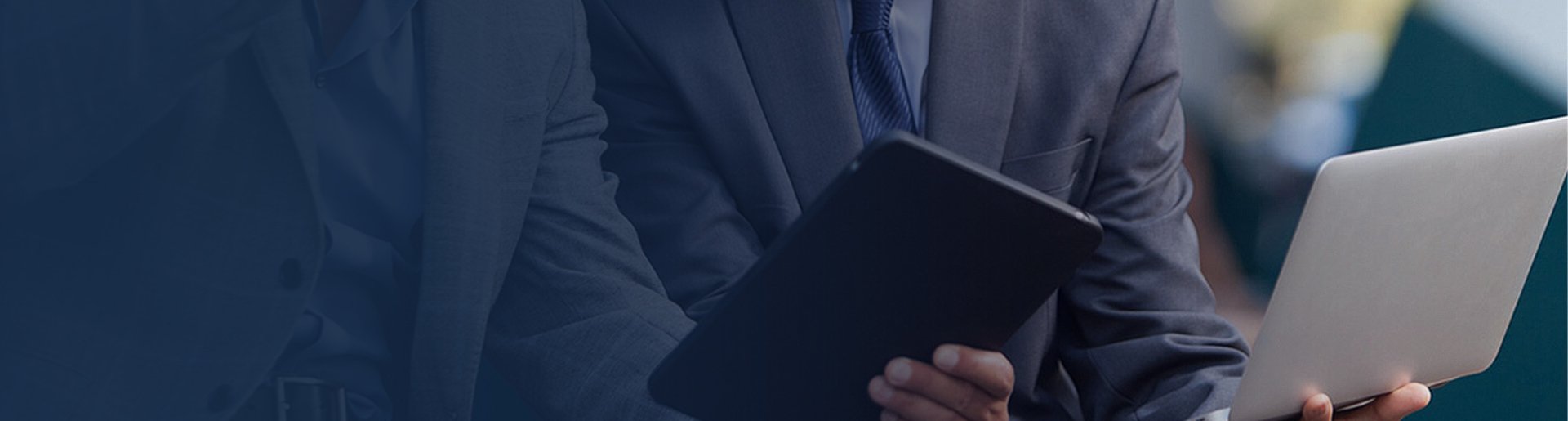
Comparison of surface treatment processes for metal stamping parts: powder coating vs. galvanizing
In the highly competitive field of metal manufacturing, the surface treatment process of metal stamping parts is crucial. It not only affects the appearance of the product, but also the performance and service life of the product. As a Chinese custom metal parts manufacturer with 28 years of rich experience, we have a deep understanding of the characteristics and advantages of different surface treatment processes. Today, let us take a deep look at the powder coating and galvanizing of metal stamping parts to help you make a smarter choice in production.
1. The process principle is revealed
Powder coating
Powder coating, that is, electrostatic powder spraying, is to charge plastic powder through high-voltage electrostatic equipment, and under the action of the electric field, it is evenly adsorbed on the surface of the metal stamping part to form a powder coating. Subsequently, the workpiece with the powder coating is sent to a high-temperature furnace for baking. The powder particles melt, level and solidify at high temperature, and finally form a dense and hard protective coating on the surface of the workpiece. This coating not only has good corrosion resistance, but also provides a rich variety of color and surface texture options.
Galvanizing
Galvanizing is to coat a layer of zinc on the surface of metal, alloy or other materials to achieve the effect of beauty and rust prevention. The main methods used are hot-dip galvanizing and cold-dip galvanizing. Hot-dip galvanizing is to immerse the workpiece in molten zinc liquid to form a metallurgical bond between the zinc layer and the surface of the workpiece; cold-dip galvanizing is to use electrolytic equipment to deposit a zinc layer on the surface of the workpiece through electrochemical principles. The galvanized layer can effectively isolate the metal from the external environment and prevent the metal from being oxidized and corroded.
2. All-round performance comparison
Corrosion resistance
Spray coating: Under normal conditions, the spray coating can provide reliable protection and has good corrosion resistance. Its salt spray corrosion resistance can usually reach about 500-1000 hours. However, once the coating is damaged, moisture and oxygen may penetrate into the metal surface, causing local corrosion.
Galvanizing: Especially hot-dip galvanizing, its corrosion resistance is extremely excellent, and it performs well in harsh outdoor environments and humid environments. The salt spray corrosion test of the hot-dip galvanized layer can reach more than 1,000 hours, and it can play a long-term protective role even in extreme environments such as marine atmosphere. This is because the electrode potential of zinc is lower than that of iron. When the zinc layer is damaged, zinc will be corroded first, thereby protecting the internal metal matrix. This protective effect is called "sacrificial anode protection".
Wear resistance
Spray coating: The spray coating has a certain wear resistance and can resist slight friction in daily use. However, in a high-wear environment, the wear resistance of the spray coating is relatively weak, and wear and scratches may occur.
Galvanized treatment: The galvanized layer has strong wear resistance and can withstand high-intensity friction and wear. It is suitable for metal stamping parts that need to withstand long-term friction, such as building hardware, mechanical parts, etc.
Appearance effect
Spray coating: The spray coating process provides a rich selection of colors, from bright bright colors to low-key matte colors. At the same time, various unique surface effects, such as wood grain, stone grain, metal texture, etc., can be achieved through special powder formulas and processes, which greatly meet the personalized needs of different customers for appearance.
Galvanized treatment: The metal surface after galvanizing usually presents a silver-gray metallic luster, and the appearance is relatively simple. Although different colors can also be obtained through passivation treatment and other methods, there is still a certain gap in the diversity of colors and surface effects compared with spraying treatment.
Adhesion and hardness
Spraying treatment: The spray coating has good adhesion to the metal surface, but when encountering a large external impact or deformation, the coating may fall off. The hardness of the spray coating layer can generally meet the requirements of daily use, but in some application scenarios with extremely high hardness requirements, it may be slightly insufficient.
Galvanized treatment: The galvanized layer forms a metallurgical bond with the metal matrix, and the adhesion is extremely strong. Even when subjected to large external force deformation, it is not easy to fall off. The galvanized layer has a high hardness and can effectively protect the metal surface from scratches and wear.
3. Cost Analysis
Material Cost
Plastic Spraying: The main material is plastic powder, and the cost is relatively low. The prices of plastic powders of different brands and qualities vary, but in general, the material cost is at a medium level in the surface treatment process.
Galvanizing: The main material of galvanizing is zinc. Hot-dip galvanizing uses a large amount of zinc, and the material cost is relatively high. Although cold galvanizing uses less zinc, due to its complex process, the comprehensive cost is not low.
Processing Cost
Plastic Spraying: The plastic spraying process requires special electrostatic spraying equipment and curing furnaces, and the equipment investment is large. However, in mass production, due to its high production efficiency, the processing cost per unit product will be reduced. In addition, the powder generated during the plastic spraying process can be recycled and reused, further reducing the production cost.
Galvanizing: Hot-dip galvanizing requires high-temperature equipment and a large amount of zinc liquid, which consumes a lot of energy and has a high processing cost. The processing process of cold galvanizing is relatively complicated, and the electrolytic conditions need to be strictly controlled. The processing cost should not be underestimated. Moreover, the wastewater and waste gas generated during the galvanizing process need to be treated for environmental protection, which also increases part of the cost.
4. Application scenarios are very different
Spraying treatment
Due to its rich colors and good corrosion resistance, spraying treatment is widely used in interior decoration, furniture manufacturing, electronic and electrical housings and other fields. For example, the housings of various household appliances, parts of office furniture, metal decorations for interior decoration, etc., are often sprayed to meet people's needs for beauty and durability.
Galvanizing treatment
Galvanizing treatment plays an important role in outdoor construction, bridges, power facilities, automobile manufacturing and other fields due to its excellent corrosion resistance and wear resistance. Like scaffolding for construction, steel structures of bridges, parts of power towers, chassis and body structures of automobiles, etc., all need to be galvanized to ensure long-term performance in harsh environments.
5. How to choose a suitable surface treatment process?
When choosing the surface treatment process for metal stamping parts, multiple factors need to be considered comprehensively:
1. Use environment: If the metal stamping parts will be used in harsh outdoor environments or humid and corrosive environments, galvanizing is a better choice; in indoor environments, when the appearance color requirements are high, spraying treatment is more advantageous.
2. Performance requirements: For applications that require high wear resistance and strong adhesion, galvanizing is more suitable; if you pay more attention to appearance and general corrosion resistance, spraying can meet the needs.
3. Cost budget: In terms of cost, the material and processing costs of spraying are relatively low, which is suitable for cost-sensitive projects; while galvanizing, although more expensive, has more significant long-term value in cases where performance requirements are extremely high.
As a professional metal parts manufacturer, we will provide personalized surface treatment solutions based on the specific needs of our customers and the application scenarios of our products. Whether it is spraying or galvanizing, we use strict quality control and exquisite craftsmanship to ensure that every metal stamping part meets excellent quality standards.
In the world of metal manufacturing, choosing the right surface treatment process is a key step in creating high-quality products. I hope that through the introduction of this article, you will have a deeper understanding of spraying and galvanizing of metal stamping parts, and be able to make wise decisions in production. If you have any questions about metal parts production and surface treatment, please feel free to contact us, we will be happy to serve you.