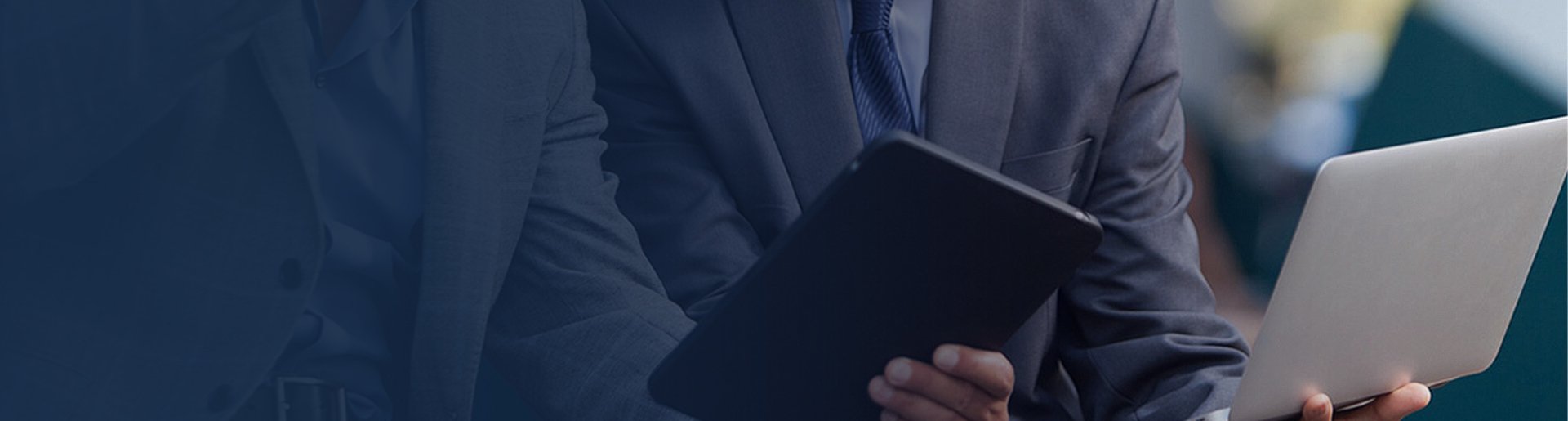
Kailai Machinery fully analyzes the application of hot forming technology in metal stamping: manufacturing breakthroughs from principle to practice
In the field of metal manufacturing, metal stamping, as one of the core processes, has always sought breakthroughs in the balance between precision and efficiency. Hot forming technology gives metal stamping stronger material adaptability and performance improvement space. Kailai Machinery, as a manufacturer of customized metal parts with 28 years of experience, is well aware of the innovative significance of hot forming to metal stamping - it is not only a simple combination of "heating + stamping", but also a system engineering that integrates material science, temperature control technology and precision machining. The following will comprehensively analyze the application of hot forming in metal stamping from process principles, complete processes to technical points.
1. The core logic of hot forming: Why can high temperature change the boundary of metal stamping?
The essence of metal stamping is to plastically deform metal materials through external forces, but cold stamping is limited by the yield strength of the material at room temperature, and often faces problems such as cracking and springback in the processing of complex shapes or high-strength parts. The breakthrough of hot forming is that metal materials enter a "superplastic state" through precise heating. When the temperature reaches the recrystallization temperature of the material (such as 800-950℃ for steel and 450-550℃ for aluminum alloy), the yield strength of the material decreases by more than 50%, and the plasticity increases by 3-5 times, making deep drawing and complex curved surface forming that were originally impossible to complete by cold stamping possible.
At the same time, the "dynamic phase change" at high temperature provides an opportunity for performance improvement. Taking automotive boron steel (22MnB5) as an example, after hot stamping and quenching, the austenite inside the metal is transformed into martensite, and the tensile strength jumps from 600MPa of cold stamping to more than 1500MPa. This is also the reason why hot forming is irreplaceable in the manufacture of safety parts.
2. The complete process of hot forming: seven key links from materials to finished products
1. Material screening and pretreatment
Hot forming of metal stamping has specific requirements for materials, and not all metals are suitable. High-strength alloys are the mainstream choice:
- Steel: mainly boron-containing steel (such as 22MnB5), whose boron content (0.0005-0.003%) can significantly improve hardenability;
- Aluminum alloy: 6xxx series (such as 6061) can reach a strength of more than 300MPa through hot forming + aging treatment;
- Special scenarios: Titanium alloys (such as Ti-6Al-4V) are used in the aerospace field, which need to be heated under inert gas protection to prevent oxidation.
The pretreatment stage needs to remove oil stains on the surface of the material, and spray high-temperature protective coatings (such as aluminum silicon coatings) according to needs, with a thickness of 5-15μm, which can prevent oxidation during heating and reduce stamping die wear.
2. High-frequency induction heating: precise temperature control is the core
Heating is the "soul step" of hot forming, which directly determines the success or failure of subsequent metal stamping. At present, the mainstream adopts high-frequency induction heating (frequency 20-400kHz), which has the following advantages:
- Fast heating speed (up to 100℃/s), avoiding long-term high temperature of materials leading to coarse grains;
- High temperature uniformity (within ±5℃), real-time monitoring by infrared thermometer to ensure that the temperature difference between different areas of the plate does not exceed 10℃.
The heating parameters of different materials vary significantly:
- Boron steel needs to be heated to 880-950℃ and kept warm for 3-5 minutes to ensure complete austenitization;
- Aluminum alloy is heated to 480-520℃, and the holding time is shortened to 1-2 minutes to prevent overburning.
3. Fast transfer: "hot connection" racing against time
The heated material needs to be transferred to the stamping die within 5 seconds - for every 10℃ drop in temperature, the yield strength of the material will increase by 5%, which directly increases the difficulty of stamping. Therefore, the production line needs to be equipped with a servo robot arm with a positioning accuracy of ±0.5mm to ensure that the material is accurately fed into the mold cavity.
4. Mold design: "Dual carrier" of stamping and quenching
The biggest difference between hot forming molds and ordinary cold stamping molds is the integrated cooling system:
- Spiral or grid cooling water channels need to be opened on the cavity surface with a spacing of 15-20mm to ensure uniform cooling;
- The cooling medium uses warm water at 50-80℃ (flow rate 2-3m/s), and the mold and parts are closely fitted to achieve "stamping + quenching" simultaneously.
Taking the hot stamping mold of the automobile B-pillar as an example, its working surface hardness must reach HRC50 or above, and the surface roughness Ra≤0.8μm, which not only ensures wear resistance but also reduces scratches on the surface of parts.
5. Stamping: Precise matching of pressure and speed
Parameter settings in the metal stamping stage need to be adapted to the material temperature and part shape:
- Stamping pressure: Select a 1000-3000 ton press according to the material thickness (0.5-3mm) and complexity. Complex parts need to be stamped in multiple steps (such as preforming first and then finishing);
- Stamping speed: Controlled at 10-30mm/s. Too fast will easily lead to uneven material flow, and too slow will increase deformation resistance due to cooling.
For parts with bosses and holes, punching, flanging and other processes can be completed simultaneously during the stamping process to reduce subsequent processing steps.
6. Quenching and cooling: the "key step" to lock the material performance
After stamping, the parts need to be kept in the mold for 10-30 seconds and quickly cooled down by the cooling system:
- The cooling rate needs to be ≥50℃/s (boron steel requirement) to ensure the transformation of austenite to martensite;
- The final temperature needs to be reduced to below 200℃ to avoid performance fluctuations due to residual heat after the parts are ejected from the mold.
After cooling, the robot arm takes out the parts, at which time the parts have more than 80% of the final strength.
7. Post-processing and quality inspection
- Surface cleaning: Shot peening is used to remove the oxide scale, and pickling and passivation are performed when necessary to improve corrosion resistance;
- Accuracy correction: Laser cutting and trimming are used for complex contour parts, and the dimensional accuracy can reach ±0.1mm;
- Performance testing: Use Rockwell hardness tester to test hardness (HRC45-50 after hot forming of boron steel), tensile testing machine to verify tensile strength, and three-coordinate measuring machine to test shape and position tolerances.
3. Technical difficulties and breakthroughs of hot forming in metal stamping
1. Temperature field uniformity control
Challenge: The edge and center of the plate are prone to a temperature difference of more than 10°C, resulting in uneven strength of various parts of the parts.
Solution: Adopt "zone heating" technology, independently control the temperature through multiple sets of induction coils, and optimize the heating path in combination with finite element simulation to control the temperature difference within 5°C.
2. Mold wear and life
Challenge: The friction coefficient between the material and the mold increases at high temperatures, and the mold life is only 1/3 of that of the cold stamping mold.
Solution: Spray WC-Co coating (thickness 50-100μm) on the mold surface, with a hardness of more than HV1200, which increases the service life from 50,000 times to more than 150,000 times.
3. Cost balance
Challenge: The investment in hot forming equipment is 3-5 times that of cold stamping, and the economic efficiency of small batch production is poor.
Solution: Develop a "flexible hot forming production line" to achieve efficient production of multi-variety, small and medium batch parts through rapid mold change technology (mold change time <10 minutes).
As a company that has been deeply engaged in metal stamping for 28 years, Kailai Machinery has always regarded the iteration of hot forming technology as its core competitiveness - from the self-developed zone heating system to the flexible molds that adapt to multiple materials, every step of innovation is aimed at providing customers with customized metal parts with "higher strength, more accurate precision and better cost".
The value of hot forming lies not only in breaking through the process boundaries of cold stamping, but also in redefining the performance upper limit of metal parts. In the future, with the development of intelligent temperature control and lightweight materials, hot forming will play a more critical role in metal manufacturing, and we will continue to explore and let this technology create value for more industries.
If you have any needs for hot-formed metal stamping parts, please contact us as soon as possible, and we will develop a one-to-one metal stamping solution for you to meet your needs!